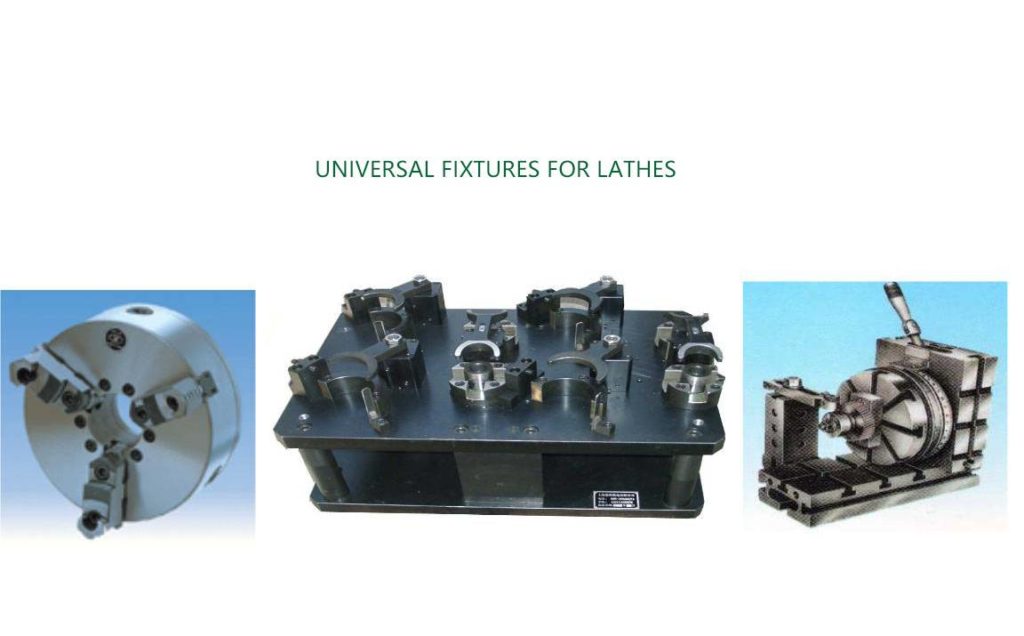
Type, structure and use of universal fixtures for lathes
1. Driver center
(1) in and out of the dial top in order to shorten the clamping time, can be used in and out of the dial top class, the cone teeth on the top cone can be embedded with artificial parts, dial the workpiece rotation. The cone Angle is generally 60. , hardness of 58 ~ 60HRc: external dial top, used for clamping sleeve type workpiece, it can process the outer circle in a clamping. Internal toggle center for clamping shaft type workpiece.
(2) End face toggle can use end face dial claw to drive the workpiece rotation. The workpiece is still centered at center}L. The advantages of this top: can quickly clamp the workpiece, and can process the entire outer surface in a single installation.
2. Spring collet and spring mandrel
Spring collet and spring mandrel are a centering clamping device. It can be centering, fork clamping, is a typical fixture commonly used on lathes. Its biggest characteristic is the large expansion in diameter (the expansion can reach L 5 ~ 5mm), therefore, the scope of application is larger. Step spring mandrel, its expansion is L ~ 2mm. In order to make the spring coat L convenient, in the screw 2, rely on the screw small steps to drive the spring coat together to loosen
Cutting tool material
At present, the commonly used turning tool materials are high speed steel, carbide, coating tool materials and super hard tool materials. Performance requirements for turning tool materials. Turning tool cutting part in the very high cutting temperature work, continuous strong friction, and withstand a lot of cutting force and impact, so turning tool cutting part of the material must have the following basic properties:
(1) high hardness tool material hardness must be higher than the hardness of the workpiece material. In this way, the tool can remove excess metal from the workpiece. Currently, the hardness of the tool material should be greater than or equal to 60HRc at room temperature.
(2) the higher the hardness of the tool material, the better the wear resistance. The higher the hardness of the hard points in the tool material organization, the more the number, the more uniform distribution. The better wear resistance.
(3) sufficient strength and toughness tool material strength generally refers to bending strength. Tool material toughness generally refers to the impact toughness. In the process of cutting, the cutting tool is always affected by cutting force, impact, vibration, when the tool material has enough strength and toughness, can avoid the tool fracture, collapse edge.
(4) high heat resistance tool material heat resistance is better, allowing the higher cutting speed when cutting, is conducive to improve the processing quality and improve productivity, is conducive to prolong the tool life.
(5) Good technology technology refers to the material cutting machinability, forging, welding, heat treatment and other properties. The tool material has good process property and is convenient for tool manufacturing.